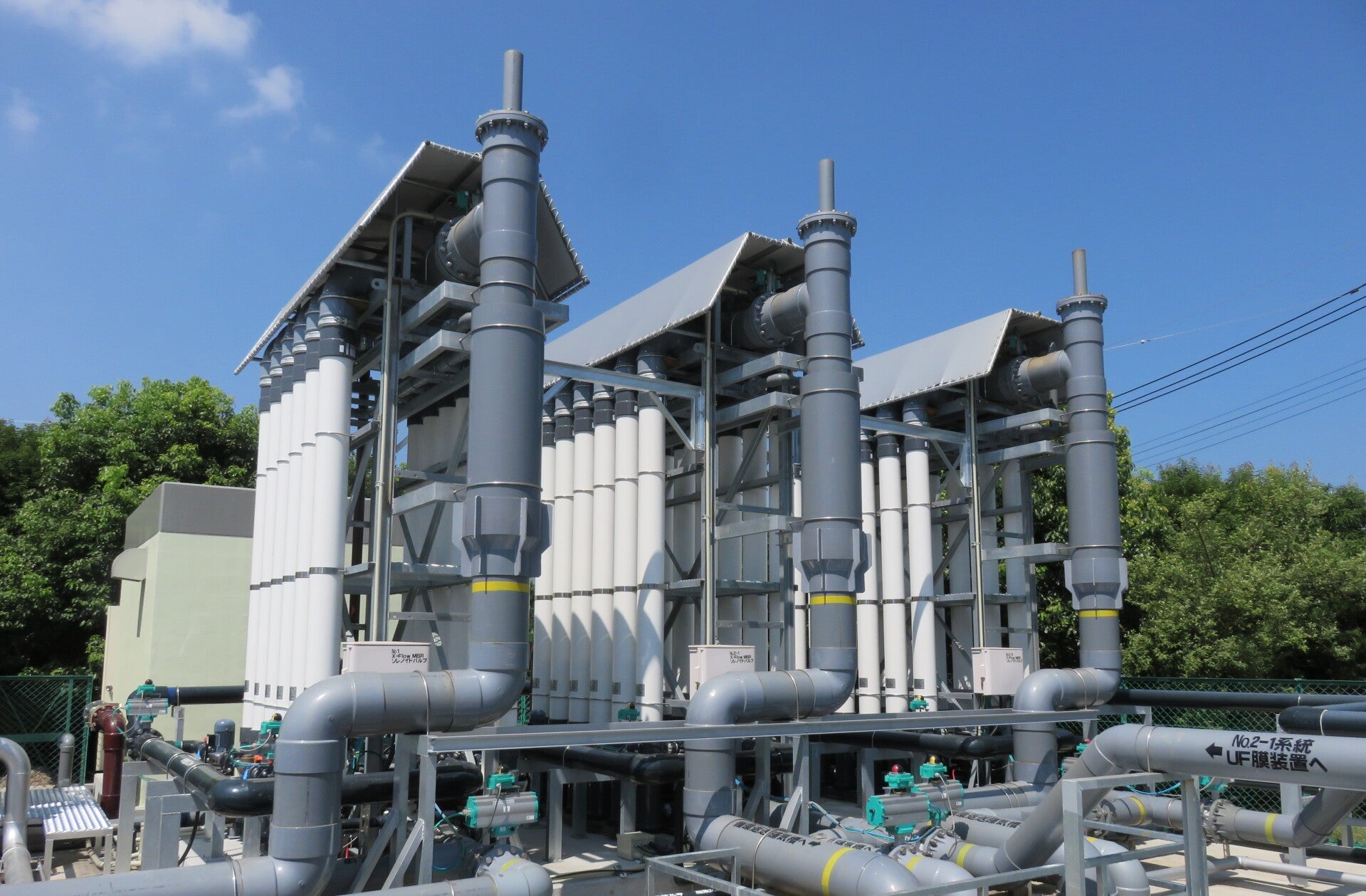
Bring expert membrane knowledge to your table
The Company
Membranes are widely used in various challenges involving separation and concentration. Circularity, the principle of reusing or recycling valuable resources, is becoming increasingly important. Membranes can play a significant role in achieving successful circular solutions.
A thorough understanding of the possibilities and proper use of membranes is essential to make their application worthwhile.
With the expert knowledge at Membron Services, independant support is offered throughout all relevant processes, with any membrane. From initial evaluations of membrane use, through basic engineering design, advising during tender sessions and developing process schemes or resolving hiccups in operating plants, troubleshooting and/or proces optimization.
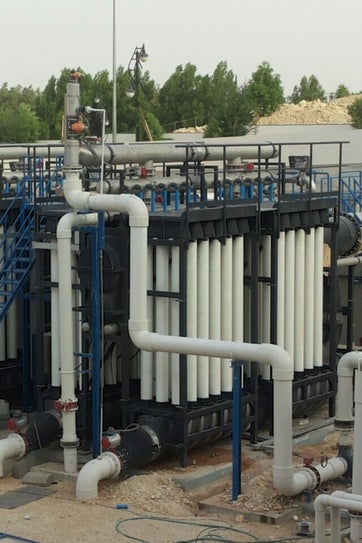
Services
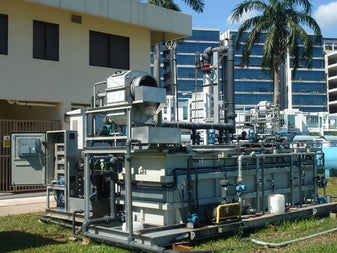
Application and Piloting Engineer
The use of membranes starts with defining the desired separation goal, followed by application research and piloting to select the right membrane and ensure sustainable use across sectors such as dairy, food, drinking water, and wastewater.
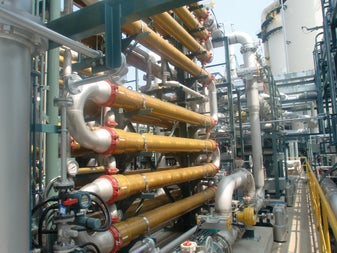
Process engineer
Once the fundamentals and key data are in place, a full-scale plant can be designed with careful attention to flux rate, concentration effects, processing time, cleaning cycles, and automation.
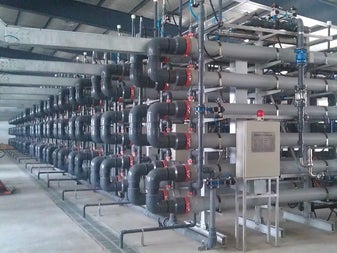
Commissioning engineer
Once the plant is built, commissioning begins with installation checks, flushing, and testing, followed by membrane setup and initial runs.
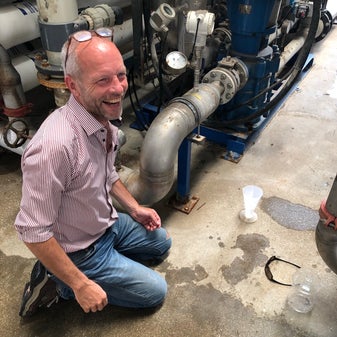
Trouble shooting
Membrane systems don’t always perform as expected, often due to issues beyond the membrane itself, which can be identified and resolved through careful assessment and practical optimization.
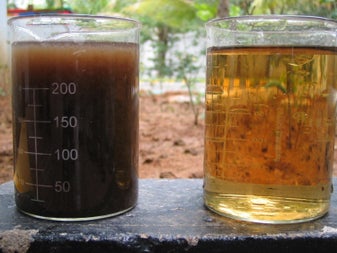
Training in membrane technology
Membrane technology is essential in separation processes and effective training helps users apply it correctly and avoid common pitfalls.
Ronald van ‘t Oever ‘who is this guy?’
My first membrane experience was a training in 1992 with Rhone Poulenc on the Pleiade system and Carbosep membranes, during my time at Terlet Machine Factory, in support of introducing these systems to the Dutch market.
Although my time at Terlet came to an end, my full commitment to membrane applications truly began when I joined the Membrane Business Unit of Stork Friesland. Over the years, I progressed through various roles such as pilot engineer, process engineer, commissioning engineer, and later sales and sales support and thus gaining experience in nearly every aspect of membrane technology. Initially in the food industry, later expanding in practially every other industry as well.
In the mid-1990s, we began using tubular membranes in membrane bioreactors, initially focusing on leachate treatment. When Stork Friesland became part of Norit X-Flow, both the company and the applications grew. Municipal interest in MBRs increased with the development of the Airlift MBR system. Today, hundreds of plants, including installations on cruise ships, use the MBR technology either in cross flow mode or Airlift. We also developed the first anaerobic MBRs during this period.
Since the Enschede factory was sold to Pentair, membrane plants have further evolved into long-term assets for a wide range of applications. These include oil/water separation, produced water treatment, and continued development of anaerobic MBRs.
With my knowledge and experience, I’ve contributed to the successful implementation of these technologies in many practical applications.